Materials
1.1
Structural elements
A corrugated
box consists of two structural elements: the facings
(linerboard) and the fluting structure (corrugated medium).
Linerboard can be of several types.
1.1.1 Types
of Liner
Fourdrinier
Kraft Liner - "Fourdrinier" is the name of the man who invented
the machine on which the liner is made. "Kraft", the German word
for strength, is attributed to the strength applied to pulp,
paper, or paperboard produced from wood fibers by the sulfate
process. The Kraft liner is produced from a high percentage of
pinewood (softwood) fibers which imparts toughness as softwood
fibers are longer in length than hardwood fibers and allows for
a greater interlocking effect. The sheet is made by randomly
orienting the fibers and is formed on a traveling endless wire
screen which may also be vibrated. This Kraft liner provides the
best Tear and Tensile strength properties available in the
paperboard industry today. The liner is used to package products
in all areas of the corrugated packaging and is widely known as
one of the best packaging materials available.
Cylinder
Recycled Linerboard - This liner is often called "Jute," a
misleading term since it never contains any jute fiber. The
correct reference name is "test liner" and is produced from
reclaimed fibers on a cylinder-type paper machine. Although test
liner often contains a certain proportion of virgin kraft fiber,
it is inherently weaker than kraft linerboard. Due to the
recycled fiber content, the basis weight of the recycled liner
may be increased to meet the Mullen test of comparable virgin
linerboard. The advantages of test liner is that it is
generally less expensive to manufacture than kraft liner and it
is an environmentally sound means of recycling used packaging.
The two recycled materials most often used to provide a furnish
for the test liner are:(1) double line kraft clippings: and(2)
old corrugated containers.
Double lined
kraft clipping(DLK) waste is comprised of the trim and cutouts
generated during the process of manufacturing corrugated boxes.
It is highly desirable due to its cleanliness and consistency.
Old
corrugated container(OCC) waste is generated by collecting
corrugated boxes from stores, supermarkets, etc. after they have
been emptied. Although OCC material requires extensive
cleaning, it is an important source of recycled fiber throughout
the world.
Kraft
linerboard can have up to 25% recycled fiber. The average
recycled content of linerboard in 1990 was about 12%. There is
a problem citing figures. The numbers change rapidly and the
recycled fiber content of containerboard is increasing each
year.
Schrenz - In
many parts of the world, there are packaging economies which
lack extensive forests of softwood or the foreign exchange to
import softwood fiber, In these countries the use of recycled
fibers means "whatever fiber is locally available," down to and
including "old newspaper." The "Schrenz" is of German origin
but is understood elsewhere. Liners of this kind are often seen
in the US in boxes bringing in exports. Unless colored or
covered by a layer of other fiber deposited on the surface from
a secondary headbox, the sheet has a gray appearance and is
inferior in strength characteristics.
1.1.2 Types
of Medium
Semichemical
- This type consists of hardwood fibers made by a neutral
sulfite or comparable process. "Semichemical" refers to the fact
that hardwoods are difficult to defiber, and so the defibering
process is partly mechanical and partly chemical. This variety
is the most prevalent in the US. Appearance and other
characteristics may vary, depending on the species of wood, the
method of cooking and washing, and other production techniques.
Most of this is produced on Fourdrinier machines. Some is
produced on other forming machines. All methods of forming can
make a good medium; quality depends on furnish and stock
preparation, not on formation. Semichemical medium is "virgin"
if 75% or more of the furnish is new fibers. All-hardwood sheets
are rare since the addition of some softwood, although recycled,
is desirable to give better "runnability."
Bogus - This
type of medium is based on recycled kraft waste, generally old
corrugated. The term "bogus" is unjustified since it denotes
imitation which is incorrect. When properly made, bogus can be
of high quality and equivalent to semichemical medium.
Kraft - The
use of kraft medium is limited to situations when high tear or
puncture resistance is needed. The total consumption for this
purpose is so small that the equivalent weight kraft liner board
is substituted, but it doesn't corrugate well.
Other - This
covers any fibers not described in the foregoing paragraphs and
corresponds to the comments made under the "Schrenz" heading
for liner board.
In the US
and Canada, freight rule requirements have led to the
development of standard grades of linerboard and medium. For
linerboard, "standard" is defined in terms of basis weight and
burst strength, based on kraft facings. Caliper is not specified
for liners used to make corrugated; mills allow caliper to
"float." This permits them to run their machines to optimize
other and more important characteristics.
For
corrugated medium, "standard" is defined in terms of caliper and
basis weight. The rule calls for a minimum caliper of 0.009
inch (2.29 mm) and a minimum basis weight of 26 pounds per
thousand square feet (lb./MSF) (127 g/m2).
medium is thus referred to in the trade as "nine point".
Information
on the different properties that medium can add to the board
combination can be found in the "Compression Guideline"
available from the address and phone number on the bottom of the
page.
1.2 Combined
Board Structures
There are
four basic combined board structures in the corrugated industry;
single faced, single wall (double faced), double wall, and
triple wall.
Single faced
corrugated is made up of a single corrugated medium and a
liner. It is mainly used as a protective wrap.
Single wall
or double faced board is made up of a single corrugated medium
between two liners. The medium material can be formed into any
flute height depending on the properties desired of the board or
the end use of the container. It is used in 90% of all
corrugated containers. It can be used to make box liners, pads,
shells, tubes, partitions, die cut interior forms and display
units. single wall lends itself to use in automated high speed
packaging lines because of easy bending and lower board memory
and relative dimensional stability. The advantages of this
material that it can have tailored construction to meet package
use and requirements. It has superior die cut workability and
dimensional precision and high strength to material ratio.
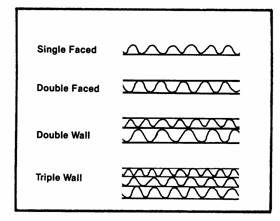
Double wall
is made up of three liner elements and two corrugated mediums.
the medium, like single wall, can be formed into any combination
of flute configurations. The combination of fluting and the
weights of the liners used is determined by the use of the board
or the demands to be made on the container in performance. It
is used in packaging of heavy products, bulk material, items
which require the extra strength and puncture resistance. The
high compression strength and flexural stiffness in relation to
single wall, make the material outstanding for inner packing,
corner posts and bulge resistant applications.
For reasons
of economy, symmetrical flute constructions in double wall
boards, such as AA or CC are infrequently used. Mainly for
production flexibility, corrugated box plants run both fluting
rollers (A, B, and/or C) on the corrugator to produce two
different flutes in the final sheet.
Triple wall
is the most complex and least used of the three. It consists of
4 liners and 3 corrugated mediums. Using various strength liners
and mediums, this material can be tailored to any packaging
demand. It is used where maximum stack strength and sidewall
strength is required.
1.3 Flute
Orientation
Boxes are
normally made with the flute direction running vertically.
This provides better stacking strength on the vertical
direction.
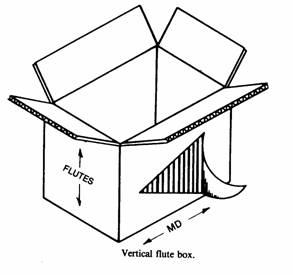
For a few
commodities, shipping containers may be made with the flutes
running horizontally.
Such boxes
are usually end-opening. They are stacked, stored or shipped
laying on their side because this is the direction of their
greatest strength.
1.4 Flute
Structure
There are
four basic fluted board heights available in conventional
corrugated board...A, B, C, and E flutes.
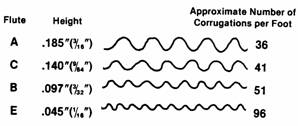
2.
Corrugated Manufacturing
2.1
Formation
The
corrugator machine flutes the medium, places liquid starch on
the peaks of the flutes, then combines it with the liners into a
continuous web of combined board. The material is then passed
through hot "irons" causing the water to be dried out of the
starch gluing the liners and medium together. Once combined the
web passes through a slitter/scorer where the web is cut and
scores are applied in the machine direction. The last operation
on the corrugator is the cut off knife where the slit/scored
web is cut into blanks.
2.1.1
Die-cut
Corrugated
that is to be die-cut does not get scored on the corrugator and
is printed before being die-cut. Some die-cutting machines can
print the corrugated before die-cutting it, others need the
corrugated to be printed on a separate machine. The process is
simple, a plain pad of corrugated is feed into a machine where a
die (like a cookie cutter) stamps out the item. The die can
either be rotary or flat depending the item's size and quantity
being run. The die can cut, slit and scores all at the same
time depending on what type of knife or rule is used. The
cutting die's tooling cost is based on how many inches of knife
or rule is used to make the die and the type of die (i.e. rotary
dies are more expensive than flat dies).
2.1.2 Non
Die-cut
Non die-cut
items are run on machines that can be modified for each order
and do not require tooling. The most common example is a RSC
(regular slotted container) below.
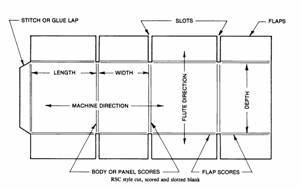
The flap
scores are put on by the slitter/scorer at the corrugator. The
resulting blank is next processed on a printer-slotter, which
prints, puts in the panel or body scores, and slots the box.
3.
General Styles
Box
dimensions are always inside dimensions (I.D.) and are stated in
sequence of Length x Width x Depth (LxWxD). The first two
dimensions mentioned are always considered the size of the
opening.
Common
drawings of box styles can be found in the format drawings at
the end of this section or in the Fibre Box Handbook which can
be ordered through PPO order or call Corporate Packaging
Programs at the number on the bottom of this page.
4.
Design Concepts
4.1 Optimum
Design
Every
Packaging Engineer endeavors to arrive at a design which will be
"optimum." The question is, optimum with respect to what? At
what point does the process of optimizing begin?
The answers
to these questions involve an understanding of what the function
of the package is to be, the conditions and circumstances of its
use, and balance between sometimes conflicting goals.
Circumstances also dictate where the optimizing process begins.
If the package is designed by the Packaging Engineer, the option
of selecting the best material will most likely not be part of
the process. The Packaging Engineer usually has neither the
means to control that process nor the information needed to
implement it. Therefore, the more collaboration there is between
the Packaging Engineer and the package maker, the earlier in the
chain the process of optimizing can start.
4.2
Constraints
The number
of choices and options available is large, but only within
certain constraints. Regulations, such as freight rules, the
Hazardous Materials Regulations, and specification requirements
may mandate limits with respect to box size, test criteria,
contents weight, board combination, etc. Your
equipment and the storage, handling and shipping environment
must be considered.
The nature,
shape and fragility of the product help to define what is
optimum.
Before going
on to the specifics, it should be clear that it is not suggested
that all steps outlined in this section are part of the design
process of every package.
4.3 Board
Structure
The basic
fact to remember is the way corrugated functions as a structure
under load.
When a
corrugated column is under load, the structure bends until it
buckles. In a box with contents this bending generates
compression stresses in the inside liner, while the outside
liner is in tension.
Therefore,
if the board combination is unbalanced, the heavier or rather,
the stiffer liner (the two usually go together) should be the
inside liner. For printing it is best to have the heaviest on
the outside.
On double
wall board there is an additional factor to be considered. The
center liner, even if it is not commonly at the exact center -
because most double wall construction do not have identical
flute contours - is near the neutral axis where the compression
contribution is minimal. Therefore, the optimum board
combination is the one where the inside liner is the stiffest,
the weakest liner is in the center, and the second stiffest
liner is on the outside. The center liner needs only to be
strong enough to hold the flute structure in place. The more
weight per stiffness one can concentrate on the inside, the
better, with due regard for other characteristics, of course. In
other words, when it comes to double wall constructions, one can
juggle board combinations at will, the only constraint being
that the minimum combined weight of facings must comply with the
freight rules.
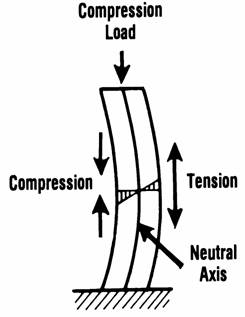
Schematic of
stresses in a compressed corrugated panel.
Along the
same lines, a thinner column bends more easily than a thicker
one. Therefore, all things being equal, any step towards
maximizing caliper is a step towards optimizing the box. The
chief mechanism for achieving this is the flute structure.
In single
wall boards the progression from best to worst in (top to
bottom) compression is from A to C to B, except that caliper
loss sustained in fabrication tends to negate the advantage of
A-flute, a fact of increasingly greater importance as medium
becomes softer. For general good performance with regular 26 lb.
medium, C flute is better, combining as it does the advantages
of B flute with those of A flute.
4.4 Die Cut
Holes
A box is
only as strong as its weakest column. Die cut holes, slots and
slits are normally the weakest part of any corrugated shipping
container. The removal of material, or crushing of the
corrugated structure, causes the surrounding area to take up the
additional stress causing it to fail before the rest of the
container. This is multiplied when the die cut is placed near
the strongest part of the box, a corner or an edge.
Die cut
holes can only weaken a shipping container's design and should
be eliminated whenever possible. However, sometimes the need
for localization holes (the customization of products for
international requirements) is unavoidable. The Packaging
Engineer should strive to design a structurally sound method for
localization.
4.5 Printing
Printing can
reduce the strength of a shipping container just as efficiently
as a die cut hole can. Printing words and/or graphics on the
outside of a container can cause damage. The pressure from the
printing rollers needed to obtain a good print will crush the
flute structure weakening the board.
A study
conducted by Colgate Palmolive Peet Company shows that a
corrugated container starts losing compression strength when
printing exceeds 20% coverage.
Laboratory
test results on printed and unprinted boxes will nearly always
favor the unprinted box. Laboratory technicians who suspect that
excessive printing pressure may have been the major cause of
failure may dissect box panels after compression tests and
caliper board thickness on the printed and unprinted areas. The
difference will be "printing pressure." Typically, the results
will be rated against the following standards: A-flute - .015",
B-flute - .013" and C-flute - .011". If these maximums are
exceeded, the box maker should be advised to make adjustments on
their printer.
4.6 Size
It is
important to control the size of the container so it can fit
properly on to a 40" x 48" pallet. If the container is designed
too large then there will be overhang. Overhang prevents the use
of the strongest elements of the container, the corners and
edges. The stress is placed on the bottom panel which fails.
Another possible problem with oversized container is that they
are placed on their sides to obtain optimum cube on a pallet.
This places the corrugation of the body panels parallel to the
compressive forces reducing the strength of the container. The
flap panels become the load bearing surface and quickly fail.
Most recent
tests, under tight laboratory conditions and pre-conditioning of
the packaging, showed a 50% difference in strength between a box
with vertical fluting vs. horizontal fluting.
4.7 Inserts
Corrugated
insert are mainly used to separate products but can be employed
to increase the structural strength of a shipping container.
Information on the effects of some of the more common corrugated
interiors on box compression can be found in the "Compression
Guideline" available from Corporate Packaging Engineering
(address and phone number on the bottom of the page).
5.
Standards
5.1 United
States Standards
The
standards that control how corrugated boxes are made in the US
are "Railroad Classification Rule 41" and "National Motor
Freight Classification Item 222". The most effective way to get
a copy of these rules along with other useful information about
corrugated (which some of this section came from) order the
Fibre Box Handbook.
These
standards, Rule 41 & Item 222, are based upon some very basic
tests that do not represent the corrugated container's actual
strength. These tests are the Mullen burst test (which tests to
see how much pressure it takes to pop a hole in the corrugated)
and minimum combined weight of facings (which looks for how much
the corrugated weights per thousand square feet and determine if
the correct weight of liners were used). Since neither of these
tests correlates to how the container will perform, the
corrugated industry is investigating edge crush testing as a
replacement for the Mullen burst test. The edge crush test
requirement will allow the designer to choose the type of
corrugated bases on stacking strength requirements
.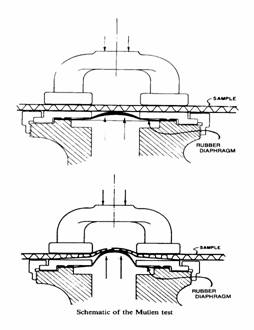
5.1.1 Box
Maker's Certificate
A corrugated
container must bear a legitimate box maker's certificate in
order to qualify for shipment by common carrier. The
certificate guarantees that the box was made to specifications
of the Fibre Box Association, and in conjunction with the
requirements of the various freight classification agencies such
as the American Trucking Association, Inc.
The
certification must include the results of a burst, puncture, or
edge crush test; the results of the minimum combined weight of
facings; the size limit; and the gross weight.
For more
information regarding the information contained within the Box
Maker’s Certificate refer to the Fibre Box Handbook which can be
ordered through PPO order or contact Corporate Packaging
Programs at the phone number at the bottom of the page.
5.2
International Standards
Standards
for corrugated in the international community differ from
country to country. Therefore, it is difficult to present that
data here.
It has been
observed that the US Rule 41 and Item 222 will meet most other
countries requirements.
6.
Closure Requirements
If boxes are
improperly or carelessly closed, their carrying qualities are
lessened - an invitation to pilferage and to other loss or
damage.
6.1 Closure
Performance
The package
closure's primary function is that of containment. In addition,
the closure must:
·
Maintain interior cleanliness and ensure that contents remain
intact during shipping and handling.
·
Permit access to the contents for inspection without destroying
the usefulness of the container.
·
Not
create a safety hazard when the package is opened or allowed
contents to spill.
·
Conform to all applicable carrier regulations.
6.2
Preferred Closure Materials and Methods
Preferred
materials for closure of corrugated cartons are reinforced (non-asphaltic)
water-activated gummed paper tape (kraft color) or
pressure-sensitive transparent plastic tape, minimum width of
2".
Strapping is
an acceptable form of closure and is commonly used when securing
a container to a pallet.
Other
sealing techniques, such as staples and adhesives, usually cause
significant structural damage when cartons are opened along with
becoming a possible safety hazard and therefore should not be
used.
Containers
for contents weighing less than 70 lb. can be sealed with only
two strips of tape on the top and bottom center seams. The tape
should extend a minimum of 2 1/2' over the edge of the
container. Heavier contents requires additional tape along the
other top and bottom edge seams.
|